You may have seen Jarron flying one of these at Sunset last year. Or maybe you saw us flying them at Los Banos in 25mph winds? If you didn't, allow me to explain, these are seriously fun little planes! You can fly them in a tiny place, they are a hoot to fly and mess around with, they are nearly impossible to kill and are a riot when you have a few other pilots flying them at the same time. They are at home on just about any slope from micro lift up to maybe 30mph with some ballast slapped on the CG. They are so tiny you can always bring them with you. They are a great plane to test out a new flying area, etc.
Often times a free flight converted model flies, well, like a free flight model. But the Mini Solius actually flies like a little foamy RC plane. Loops, rolls, inverted flight are all good.
We have abused the heck out of ours in the past. Doing things like flying them into the trunk of the car, aero towing them, combating much larger models, and just plane being silly. I hope you are getting the idea here.. FUN
So being a free flight chuck glider for kids, it is up to you how you would like to convert them. We started off with 3 servos controlling the ailerons and elevator. Those were great, no complaints. Then our friend Mike R. brought his pitcheron build by the shop and it looked even better, and he reported it also flew great. We don't think it is worth the trouble or weight to control the rudder, but if that is your cup of tea, go for it.
We have these on our site here:
alofthobbies.com
or you can get them direct from Mr Multiplex.
Here are some pictures of our aileron builds. Nothing special. Just remove some foam for radio gear, run the wires, a little carbon strip for a wing spar and linkages, etc. These planes have been through the ringer! Still fly great.
Often times a free flight converted model flies, well, like a free flight model. But the Mini Solius actually flies like a little foamy RC plane. Loops, rolls, inverted flight are all good.
We have abused the heck out of ours in the past. Doing things like flying them into the trunk of the car, aero towing them, combating much larger models, and just plane being silly. I hope you are getting the idea here.. FUN
So being a free flight chuck glider for kids, it is up to you how you would like to convert them. We started off with 3 servos controlling the ailerons and elevator. Those were great, no complaints. Then our friend Mike R. brought his pitcheron build by the shop and it looked even better, and he reported it also flew great. We don't think it is worth the trouble or weight to control the rudder, but if that is your cup of tea, go for it.
We have these on our site here:
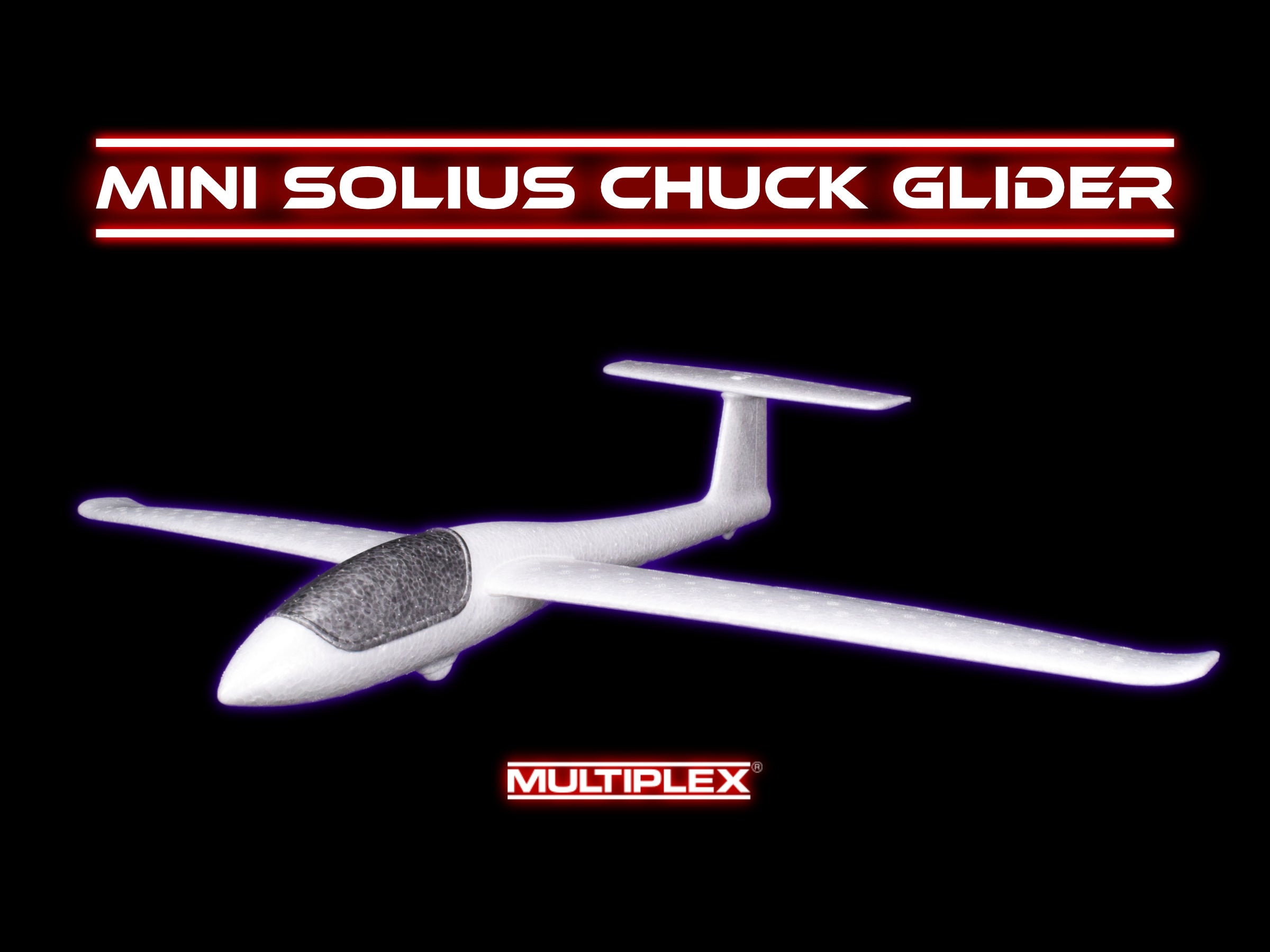
Multiplex Mini Solius Chuck Glider
These inexpensive, simple chuck gliders from Multiplex are such a hoot to play with here at the shop, we thought we'd share them with everyone! These are great planes for young kids as they are tough! Constructed of EPP foam that is so resilient you can throw it straight into pavement and it...
Here are some pictures of our aileron builds. Nothing special. Just remove some foam for radio gear, run the wires, a little carbon strip for a wing spar and linkages, etc. These planes have been through the ringer! Still fly great.
Last edited: