Turns out one of our customers has been working on a 3D printed slope gliders and offering the print files for a very reasonable price. Check him out at:
After chatting with Wayne (that name seems familiar) a bit about his planes I decided I needed to print one up for myself. He has a pretty neat approach to the planes. He offers a common fuselage and you can pick from different tail and wing designs. You can pick V-tail, cross tail with rudder, T tail. He also offers it with an electric nose option. I went with the cross tail, no rudder and 4 servo wing with the RG15 airfoil.
Paid my $20 and downloaded my files last night and put them into my slicer and started printing using some old trans orange PLA I had sitting around. I sort of ignored some of his suggested print settings as I'm not too worried about weight for our local slope. Here is what I had when I came into the office this morning.
A tiny bit of sanding and we have this (I did not use the suggested BRIM setting, no adhesion issues at all):
Some details:
I tried to use the Prusa slicer for the Horizontal tail, but it didn't do well, so off to CURA slicer and using Wayne's suggested settings, except no BRIMs. I hate Brims.
@RafaelAvila is helping to fine tune things with Cura and our Prusa printers. We are using PETG for the horizontal and wing panels. Also trying to reduce our adhesion to the printer bed as the first layer is tearing off the bed. Who needs brims? LOL
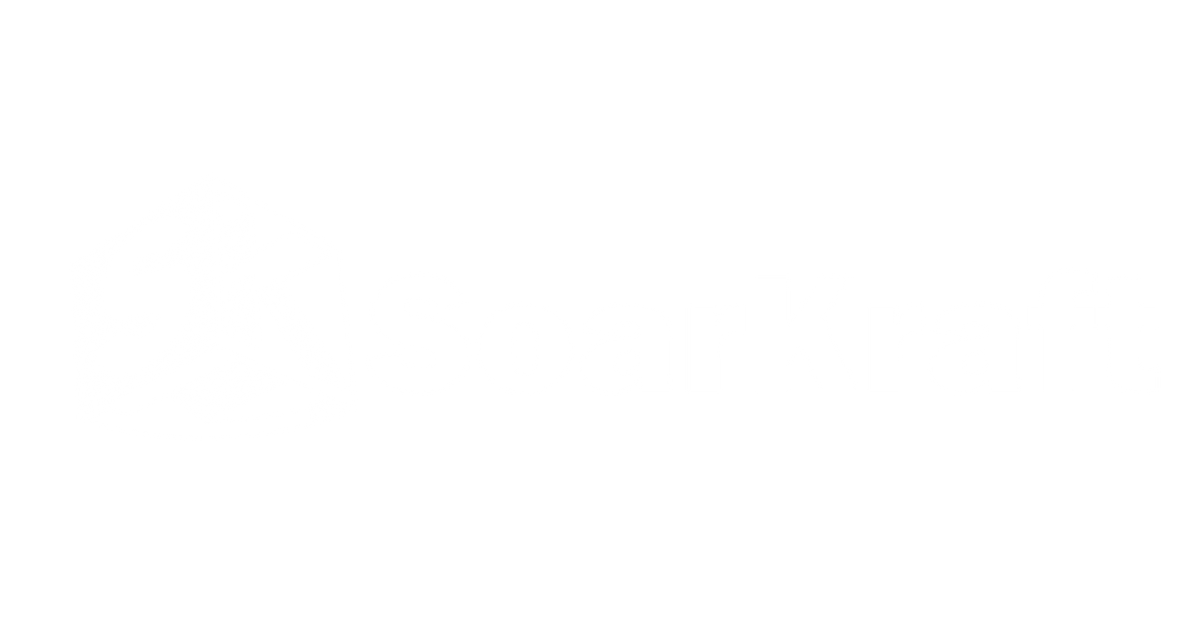
After chatting with Wayne (that name seems familiar) a bit about his planes I decided I needed to print one up for myself. He has a pretty neat approach to the planes. He offers a common fuselage and you can pick from different tail and wing designs. You can pick V-tail, cross tail with rudder, T tail. He also offers it with an electric nose option. I went with the cross tail, no rudder and 4 servo wing with the RG15 airfoil.
Paid my $20 and downloaded my files last night and put them into my slicer and started printing using some old trans orange PLA I had sitting around. I sort of ignored some of his suggested print settings as I'm not too worried about weight for our local slope. Here is what I had when I came into the office this morning.
A tiny bit of sanding and we have this (I did not use the suggested BRIM setting, no adhesion issues at all):
Some details:
I tried to use the Prusa slicer for the Horizontal tail, but it didn't do well, so off to CURA slicer and using Wayne's suggested settings, except no BRIMs. I hate Brims.
@RafaelAvila is helping to fine tune things with Cura and our Prusa printers. We are using PETG for the horizontal and wing panels. Also trying to reduce our adhesion to the printer bed as the first layer is tearing off the bed. Who needs brims? LOL